- GKN Aerospace builds new factory in Trollhättan to supply ESA with rocket engine nozzles for Ariane 6
- Trollhättan is GKN’s largest manufacturing site for engine systems employing more than 2,000 engineers, technicians and research staff
- GKN Aerospace invested EUR 78 million in R&D at the Trollhättan site in 2017
In French Guiana, an overseas territory of France located between Surinam and Brazil, a huge launch pad has entered its final construction phase at the Spaceport run by the European Space Agency (ESA) and CNES, the French Space Agency.
This concrete superstructure will soon host Ariane 6, the ESA’s new rocket launcher which is planned to lift off on a maiden flight in 2020. The mission: to secure Europe’s future access to space – and challenge SpaceX, founded by Elon Musk, in the market for rocket launches.
Meanwhile, 8,000 km away in Trollhättan, Sweden, preparations are gathering pace for a new factory at GKN Aerospace Engine Systems’ headquarters. This is where a vital component of Ariane 6’s main stage engine Vulcain 2.1 will be built – the groundbreaking SWAN nozzle – as well as turbine assemblies.
The nozzle concept was first developed by Volvo Aero, Volvo’s aerospace arm, which was acquired by the global engineering group GKN Aerospace in 2012.
Explains Martin Velander, General Manager Space, GKN Aerospace Engine Systems: “Thanks to our work 20 years ago, we can now set up a highly automated manufacturing plant in Trollhättan that incorporates three technologies; advanced milling, laser beam welding and laser metal deposition which is a niche variant of 3D printing.”
The nozzle and associated technology was developed together with the Swedish National Space Agency which continues to support the programme in its industrialisation phase.
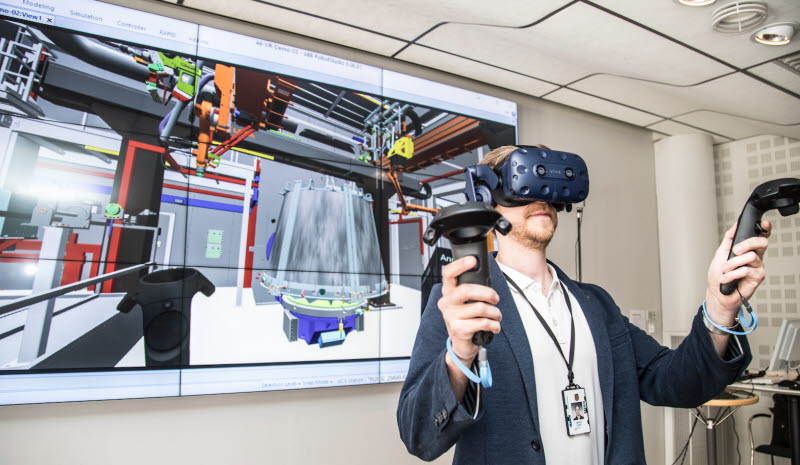
Putting satellites into orbit has become a fiercely competitive business. Slashing costs is the name of the game, and you need look no further than Sweden’s aerospace hub in west Sweden, some 75 km from Gothenburg, to get a look behind the scenes of the new space race.
“By increasing our focus on 3D printing we can reduce weight, improve the contour and create complex cooling channels on the rocket engine nozzle,” Velander continues.
Competing with SpaceX
As the space industry celebrates the 50th anniversary of the Apollo moon landing, commercial players and public consortiums are stepping up efforts to make rocket launches as affordable as possible.
With its lightweight design that reduces costs by 50 per cent, Ariane 6 is poised for success in the heavy payload category.
In addition, GKN Aerospace has announced its further role in supplying additively manufactured turbines (3D printed) for the ESA’s next generation engine called Prometheus. This will be Europe’s first reusable rocket engine which, thanks to GKN’s expertise in additive technologies, will enable a game-changing 90 per cent cost reduction. The number of parts will also be slashed from several hundred to just a few for a turbine assembly.
“SpaceX was trendsetting in every way. Most launch providers will move toward reusable low-cost rockets in the next decade,” Velander points out.
Velander’s team is due to supply ESA with 11 engine nozzles annually for Ariane 6 from the Trollhättan factory, which opens mid-2019, while phasing out Ariane 5 production.
“Each nozzle is roughly the size of a garden shed, so there’s a lot of logistics involved in addition to technical complexities. Our first Prometheus turbine will also be delivered by the end of this year.”
“Trollhättan is a great location for us,” adds Velander. “Most of our factory staff is being retrained for Ariane 6 production, but we rely on the competence of local partners for new materials and aerodynamics testing. Our R&D collaborations with Chalmers University of Technology, University West and Trollhättan’s Innovatum Science Center, where GKN has located the majority of its technology development, are fundamental to our success.”
Expanding the workshops
GKN Aerospace Engine Systems focuses on three business areas – civil aviation, military aircraft and space technology. Moreover, it reaps the benefits of synergy across a global aerospace organisation that employs 17,000 people in 15 countries, with 50 manufacturing facilities.
Of these, Trollhättan is the largest manufacturing unit for engine systems and the site employs some 2,000 engineers, technicians and research staff.
While rockets and spacecraft draw plenty of attention, GKN Aerospace’s biggest business area by far is civil aviation and solutions for jet airliners. The Geared Turbofan, co-created with Pratt & Whitney, is a recent innovation driving further expansion of turbine workshops in Trollhättan.
“You may have noticed that in the quest for fuel efficiency the fans on passenger aircraft engines are getting bigger. The Geared Turbofan allows the front fan to spin at optimal velocities which reduces fuel consumption by 15 per cent and cuts noise pollution,” says Henrik Runnemalm, Head of Research, GKN Aerospace Engine Systems.
“We began to ramp up production for this product in 2015 and expect to reach full capacity in 2020.”
Gateway to talent
Among GKN Aerospace Engine Systems’ production sites worldwide, Trollhättan is the division’s most advanced manufacturing facility in terms of robotics and automation. Increasingly, this involves Industry 4.0 connectivity and leveraging smart data.
At the same time, close collaboration with universities, public institutes, OEM’s such as Rolls-Royce and customers like Boeing, who pay for engine uptime as a service, is a cornerstone of the company’s global impact.
“We currently have 65 research students engaged in Sweden working on solving problems related to 3D printing, aerodynamics and combustion theory, among other areas. Apart from boosting our innovation capacity, this provides us with a fertile recruitment base,” Runnemalm adds.
Being a fast innovator and cutting lead times are two key priorities. For this reason, in 2017, GKN Aerospace invested EUR 78 million in research and development at the Trollhättan site. At least 500 employees now work exclusively with R&D and tech development focusing on everything from new engine concepts to 3D printing and stress-testing of new materials.
Giant leap for aviation
As a committed partner in the EU’s research programme Clean Sky, GKN Aerospace is taking decisive action to help meet international goals of reducing aero-engine emissions by 50% by 2020, and to speed up the transition to electric aircraft.
These forward strides are clearly visible on the factory floor in Trollhättan.
“Our processes are becoming more data-driven,” Runnemalm explains. “The 3D printing method we employ enables us to measure the properties of lightweight materials in real time as they are melted, from data transmitted by the laser beam”.
Recent testing has also shown that GKN Aerospace’s engines are perfectly capable of being powered by biofuels. Hybrid and electric solutions, too, are on the drawing board.
The key to decarbonizing aviation, Runnemalm concludes, is close collaboration with experts in a wide range of disciplines, and this way of working is second nature to many Swedes.
“In Trollhättan we have top talent within arm’s reach. If this was a French or Danish company for example without a presence here, I would still choose to manufacture our turbines and components in Sweden.”